Hydro Dipping, also known as water transfer printing or hydrographics, is a process used to apply decorative patterns and designs to objects. The process involves transferring a printed design onto a surface using water and a special film. The film dissolves in water, and the design is transferred onto the surface of the object, creating a unique and customizable finish.
How Hydro Dipping Works
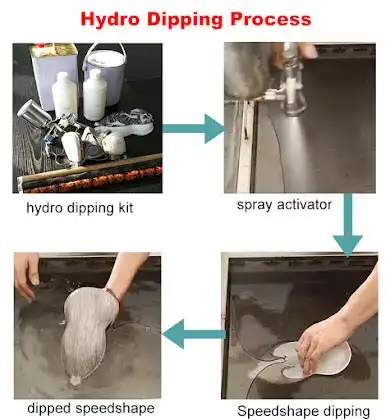
Hydro dipping is a multi-step process that involves several key steps. The first step is to prepare the object that will be dipped. This typically involves cleaning the surface of the object to remove any dirt, dust, or debris that could interfere with the dipping process. The object may also need to be sanded or primed to ensure that the design adheres properly to the surface.
Once the object is prepared, the next step is to apply the hydro dipping film. The film is a specialized material that contains the design that will be transferred onto the object. The film is typically applied to the surface of the water in a dipping tank, and it is carefully positioned to ensure that the design is aligned with the object.
The object is then carefully lowered into the dipping tank, and the film is activated. This typically involves applying a special activator solution to the film, which causes it to dissolve in the water. As the film dissolves, the design is transferred onto the surface of the object.
The object is then removed from the dipping tank, and any excess film or activator solution is carefully removed. The object is then allowed to dry, and any additional finishing steps, such as clear coating or drying, are performed as needed.
Types of Hydro-Dipping Films
There are many different types of hydro-dipping films available, and each type has its own unique properties and characteristics. The type of film that is best for a particular project will depend on the specific design and surface to that the film will be applied.
One common type of hydro-dipping film is digital film, which is a high-resolution film that can be printed with a wide range of designs and patterns. Digital film is typically used for intricate or detailed designs, as it allows for a high level of precision and accuracy.
Another type of hydro dipping film is camouflage film, which is designed to mimic the patterns and colors of natural environments. Camouflage film is commonly used on hunting and outdoor equipment, and it can provide a realistic and effective camouflage effect.
In addition to these types of film, there are also many other specialized films available, such as carbon fiber film, metallic film, and wood grain film. These films can provide unique and distinctive finishes that are not possible with traditional paint or other coating methods.
Benefits of Hydro Dipping
Hydro dipping offers many benefits over traditional coating methods, such as painting or powder coating. One of the main benefits is the ability to create unique and customizable designs. With hydro dipping, it is possible to apply almost any design or pattern onto an object, which allows for a wide range of creative possibilities.
Another benefit of hydro dipping is the high-quality finish that it provides. Hydro dipped surfaces have a smooth and even finish, and they are resistant to chipping, peeling, and other types of damage. This can provide long-lasting protection and durability for the object.
In addition, hydro dipping is a relatively quick and easy process, and it can be performed by individuals with limited experience or expertise. This makes it a convenient and cost-effective option for many applications.
Applications of Hydro Dipping
Hydro dipping is commonly used on a wide range of objects, including automotive parts, firearms, and sporting goods. The process is also frequently used on personal items, such as phones, laptops, and gaming controllers.
In the automotive industry, hydro dipping is often used to customize car parts and accessories. The process can be used to apply unique designs and patterns to wheels, grilles, and other car parts, providing a personalized and custom look for the vehicle.
In the firearms industry, hydro dipping is commonly used to customize the appearance of firearms. The process can be used to apply camouflage patterns, metallic finishes, and other designs to guns, providing a unique and personalized look.
In the sporting goods industry, hydro dipping is often used to customize sports equipment. The process can be used to apply unique designs and patterns to sports helmets, balls, and other equipment, providing a personalized and custom look for the athlete.
Overall, hydro dipping is a versatile and effective process that can be used to customize and enhance the appearance of a wide range of objects. The process offers many benefits over traditional coating methods, and it is an increasingly popular option for individuals and organizations looking to create unique and customized designs.
In addition to its many applications, hydro dipping is also a growing field, with new technologies and techniques being developed all the time. One example of this is the use of 3D printing in hydro dipping. 3D printing technology allows for the creation of highly detailed and complex designs, and it can be used in combination with hydro dipping to produce intricate and customized finishes.
Another area of growth in hydro dipping is the use of specialized films and coatings. New types of film and coating materials are being developed that offer improved durability, flexibility, and colorfastness, which can provide enhanced performance and longevity for hydro dipped objects.
In addition, new dipping tanks and equipment are being developed that can improve the efficiency and accuracy of the hydro dipping process. These new technologies can make the process faster, easier, and more precise, which can provide better results and increased satisfaction for hydro dipping customers.
Overall, hydro dipping is a growing and evolving field, and it continues to offer new and exciting possibilities for individuals and organizations looking to customize and enhance the appearance of objects. With new technologies and techniques being developed all the time, the potential applications and capabilities of hydro dipping are constantly expanding.
Despite its many benefits and applications, there are some challenges and limitations to the use of hydro dipping. One of the main challenges is the cost of the process. Hydro dipping can be a relatively expensive option, particularly for larger or more complex projects. The cost of the process can be a barrier for some individuals and organizations, which may limit its use in some applications.
Another challenge with hydro dipping is the level of expertise and skill required to produce high-quality results. The process requires a certain level of knowledge and experience, and it can be difficult for inexperienced individuals to produce professional-quality results. As a result, hydro dipping is typically performed by specialized companies or individuals who have the necessary skills and experience.
In addition, hydro dipping is not suitable for all objects or surfaces. The process is typically only effective on smooth, flat surfaces, and it may not be suitable for objects with complex shapes or contours. This can limit the range of applications for hydro dipping, and it may not be the best option for some objects or surfaces.
Despite these challenges, hydro dipping remains a popular and effective process for individuals and organizations looking to customize and enhance the appearance of objects. With the right equipment and expertise, it is possible to produce high-quality, customized finishes that are not possible with traditional coating methods.
One way to overcome some of the challenges and limitations of hydro dipping is to use alternative coating methods. There are many different coating methods available, and each method has its own unique characteristics and capabilities. By choosing the right coating method for a particular project, it is possible to achieve the desired results without the limitations of hydro dipping.
For example, one alternative to hydro dipping is powder coating. Powder coating is a process that involves applying a dry, powdery coating material to an object using an electrostatic charge. The powder adheres to the object and is then cured using heat, which creates a hard, durable finish.
Powder coating is a popular alternative to hydro dipping, as it is typically less expensive and easier to perform. The process can be performed by individuals with limited experience or expertise, and it is suitable for a wide range of objects and surfaces. In addition, powder coating offers a wide range of color and finish options, which can provide a customizable and unique look for the object.
Another alternative to hydro dipping is spray painting. Spray painting is a common coating method that involves applying a liquid coating material to an object using a spray gun. The coating material is applied in a fine mist, and it forms a uniform and even finish on the object.
Spray painting is a popular coating method, as it is relatively quick and easy to perform. The process can be performed by individuals with limited experience or expertise, and it is suitable for a wide range of objects and surfaces. In addition, spray painting offers a wide range of color and finish options, which can provide a customizable and unique look for the object.
Overall, there are many alternative coating methods available that can provide the desired results without the challenges and limitations of hydro dipping. By choosing the right coating method for a particular project, it is possible to achieve professional-quality finishes that are durable, customizable, and cost-effective.
Despite the availability of alternative coating methods, hydro dipping remains a popular and effective process for many individuals and organizations. One reason for this is the unique and customizable designs that are possible with hydro dipping. The process allows for the creation of almost any design or pattern, which can provide a truly unique and personalized finish for an object.
Another reason for the popularity of hydro dipping is the durability and longevity of the finished product. Hydro dipped surfaces are smooth, even, and resistant to chipping, peeling, and other types of damage. This can provide long-lasting protection and durability for the object, and it can be an important consideration for applications where the object will be subjected to wear and tear.
In addition, hydro dipping is a relatively quick and easy process, and it can be performed by individuals with limited experience or expertise. This makes it a convenient and cost-effective option for many applications, and it can provide professional-quality results without the need for specialized equipment or training.
Overall, hydro dipping remains a popular and effective process for individuals and organizations looking to customize and enhance the appearance of objects. With its unique and customizable designs, durability, and ease of use, hydro dipping offers many advantages over traditional coating methods.
Hydro Dipping vs. Powder Coating
Hydro dipping and powder coating are two popular processes that are used to apply decorative patterns and designs to objects. Both processes offer many benefits, such as the ability to create unique and customizable finishes, and the durability and longevity of the finished product. However, there are also some differences between the two processes, which should be considered when deciding which process is best for a particular project.
One key difference between hydro dipping and powder coating is the way that the coating material is applied to the object. In hydro dipping, the coating material is applied to the surface of the water in a dipping tank, and the object is carefully lowered into the water to transfer the design onto the object. In powder coating, the coating material is applied to the object using an electrostatic charge, and it is then cured using heat to create a hard, durable finish.
Another difference between hydro dipping and powder coating is the range of designs and patterns that are possible. Hydro dipping allows for the creation of almost any design or pattern, as the process uses specialized film materials that can be printed with a wide range of designs. Powder coating, on the other hand, is typically limited to solid colors, and it may not be possible to create complex or detailed designs using the process.
In terms of cost, hydro dipping and powder coating can be similar, depending on the size and complexity of the project. Hydro dipping may be more expensive for large or complex projects, as it typically requires specialized equipment and expertise. Powder coating, on the other hand, may be less expensive for smaller or simpler projects, as the process can be performed by individuals with limited experience or expertise.
Overall, hydro dipping and powder coating are both effective processes for applying decorative patterns and designs to objects. The right process for a particular project will depend on the specific design and surface that the coating will be applied to, as well as the cost and availability of the equipment and expertise needed to perform the process.
Environmental Impact of Hydro Dipping
Hydro dipping, also known as water transfer printing or hydrographics, is a process that is used to apply decorative patterns and designs to objects. The process involves transferring a printed design onto the surface of an object using water and a special film. While hydro dipping offers many benefits, such as the ability to create unique and customizable designs, there are also some concerns about the environmental impact of the process.
One potential environmental concern with hydro dipping is the disposal of the film materials and chemicals used in the process. The film materials used in hydro dipping are typically made from synthetic polymers, which can be difficult to break down and can have a negative impact on the environment if they are not disposed of properly. In addition, the chemicals used in the hydro dipping process, such as the activator solution, can also have negative environmental effects if they are not disposed of properly.
Another environmental concern with hydro dipping is the potential for water pollution. The process involves immersing objects in water, and if the water is not properly treated and disposed of, it can potentially contaminate natural water sources and harm aquatic life.
To address these environmental concerns, it is important for hydro dipping companies and individuals to follow proper disposal and treatment procedures for the film materials and chemicals used in the process. This can help to minimize the potential negative effects on the environment and protect natural water sources.
In addition, there are alternative coating methods available that have a lower environmental impact than hydro dipping. For example, powder coating is a process that uses dry, powdery coating materials that can be disposed of more easily than the film materials used in hydro dipping. Powder coating also does not require the use of water, which eliminates the potential for water pollution.
Overall, while hydro dipping offers many benefits, it is important to consider the potential environmental impact of the process and take appropriate steps to minimize any negative effects. By following proper disposal and treatment procedures, and by considering alternative coating methods with a lower environmental impact, it is possible to use hydro dipping in a responsible and sustainable manner.
The History of Hydro Dipping
Hydro dipping, also known as water transfer printing or hydrographics, is a process that has been used for many years to apply decorative patterns and designs to objects. The origins of the process can be traced back to the late 1960s, when it was first developed by a company called Hydro Graphics, Inc.
The original hydro dipping process was designed to apply camouflage patterns to military equipment, such as helmets and weapons. The process involved using a special film that contained the camouflage pattern, and the film was transferred onto the surface of the object using water.
Over time, the hydro dipping process was refined and improved, and it began to be used in a wider range of applications. The process was adopted by the automotive industry, and it was used to apply unique and customizable designs to car parts and accessories.
In recent years, hydro dipping has become increasingly popular, and it is now used in a wide range of industries and applications. The process is commonly used to customize firearms, sporting goods, and personal items, and it is also used in many other applications, such as decorating and product design.
The Future of Hydro Dipping
Hydro dipping is a growing and evolving field, and there are many exciting developments and innovations taking place in the field. One of the main areas of growth is the use of advanced materials and technologies in hydro dipping.
For example, new types of hydro dipping film are being developed that offer improved performance and durability. These new films are made from specialized materials that provide enhanced flexibility, colorfastness, and resistance to fading and other types of damage.
In addition, new hydro dipping equipment and technologies are being developed that can improve the efficiency and accuracy of the process. These new technologies can make the process faster, easier, and more precise, which can provide better results and increased satisfaction for hydro dipping customers.
Overall, the future of hydro dipping looks bright, and the field is likely to continue to grow and evolve in the coming years. With new materials, technologies, and applications being developed all the time, hydro dipping offers many exciting possibilities for individuals and organizations looking to customize and enhance the appearance of objects.
The Pros and Cons of Hydro Dipping
Hydro dipping, also known as water transfer printing or hydrographics, is a popular process that is used to apply decorative patterns and designs to objects. The process offers many benefits, such as the ability to create unique and customizable designs, and the durability and longevity of the finished product. However, there are also some challenges and limitations to the use of hydro dipping, which should be considered before deciding whether it is the right process for a particular project.
Pros of Hydro Dipping
- Unique and customizable designs: Hydro dipping allows for the creation of almost any design or pattern, which can provide a truly unique and personalized finish for an object.
- Durability and longevity: Hydro dipped surfaces are smooth, even, and resistant to chipping, peeling, and other types of damage. This can provide long-lasting protection and durability for the object.
- Easy to perform: Hydro dipping is a relatively quick and easy process, and it can be performed by individuals with limited experience or expertise.
Cons of Hydro Dipping
- Cost: Hydro dipping can be a relatively expensive option, particularly for larger or more complex projects.
- Requires expertise: The process requires a certain level of knowledge and experience, and it can be difficult for inexperienced individuals to produce professional-quality results.
- Not suitable for all objects: Hydro dipping is typically only effective on smooth, flat surfaces, and it may not be suitable for objects with complex shapes or contours.
Overall, hydro dipping offers many benefits and advantages, but it is not the right.
Hydro Dipping for Automotive Applications
Hydro dipping, also known as water transfer printing or hydrographics, is a popular process that is used to apply decorative patterns and designs to objects. The process is frequently used in the automotive industry, where it is used to customize car parts and accessories.
The process of hydro dipping for automotive applications is similar to the general hydro dipping process. The first step is to prepare the car part or accessory that will be dipped. This typically involves cleaning the surface of the object to remove any dirt, dust, or debris that could interfere with the dipping process. The object may also need to be sanded or primed to ensure that the design adheres properly to the surface.
Once the object is prepared, the next step is to apply the hydro dipping film. The film is a specialized material that contains the design that will be transferred onto the object. The film is typically applied to the surface of the water in a dipping tank, and it is carefully positioned to ensure that the design is aligned with the object.
The car part or accessory is then carefully lowered into the dipping tank, and the film is activated. This typically involves applying a special activator solution to the film, which causes it to dissolve in the water. As the film dissolves, the design is transferred onto the surface of the object.
The car part or accessory is then removed from the dipping tank, and any excessfilm or activator solution is carefully removed. The object is then allowed to dry, and any additional finishing steps, such as clear coating or drying, are performed as needed.
One of the main benefits of hydro dipping for automotive applications is the ability to create unique and customizable designs. With hydro dipping, it is possible to apply almost any design or pattern onto a car part or accessory, which allows for a wide range of creative possibilities. This can provide a personalized and custom look for the vehicle, and it can make it stand out from other cars on the road.
Another benefit of hydro dipping for automotive applications is the durability and longevity of the finished product. Hydro dipped surfaces have a smooth and even finish, and they are resistant to chipping, peeling, and other types of damage. This can provide long-lasting protection and durability for the car part or accessory, and it can help to extend its lifespan and improve its performance.
Overall, hydro dipping is a popular and effective process for automotive applications. The process offers many benefits, such as unique and customizable designs, and durability and longevity. By using hydro dipping, it is possible to enhance the appearance of car parts and accessories, and to create a personalized and custom look for the vehicle.
The Hydro Dipping Process: Step-by-Step
Hydro dipping, also known as water transfer printing or hydrographics, is a process that is used to apply decorative patterns and designs to objects. The process involves transferring a printed design onto a surface using water and a special film. The film dissolves in water, and the design is transferred onto the surface of the object, creating a unique and customizable finish.
The hydro dipping process consists of several key steps, which are outlined below.
- Prepare the object: The first step in the hydro dipping process is to prepare the object that will be dipped. This typically involves cleaning the surface of the object to remove any dirt, dust, or debris that could interfere with the dipping process. The object may also need to be sanded or primed to ensure that the design adheres properly to the surface.
2. Apply the hydro dipping film: The next step is to apply the hydro dipping film to the surface of the water in a dipping tank. The film is a specialized material that contains the design that will be transferred onto the object. The film is carefully positioned in the dipping tank to ensure that the design is aligned with the object.
3. Dip the object: Once the film is in place, the object is carefully lowered into the dipping tank. The film is then activated by applying a special activator solution to the film, which causes it to dissolve in the water. As the film dissolves, the design is transferred onto the surface of the object.
4. Remove the object: Once the design has been transferred onto the object, the object